Advanced Fasteners and Machining Techniques for Custom-made Manufacturing
Browsing the World of Fasteners and Machining: Techniques for Accuracy and Rate
In the intricate realm of fasteners and machining, the quest for precision and speed is a perpetual difficulty that demands thorough attention to detail and calculated preparation. From recognizing the varied selection of fastener types to choosing ideal materials that can hold up against rigorous demands, each action in the procedure plays a pivotal function in attaining the preferred outcome.
Understanding Bolt Kind
When choosing fasteners for a task, understanding the different kinds available is vital for ensuring optimum performance and dependability. Bolts come in a variety of types, each made for certain applications and requirements. Bolts are utilized with nuts to hold materials together, while screws are versatile bolts that can be made use of with or without a nut, relying on the application. Nuts, on the other hand, are internally threaded bolts that friend with screws or screws, giving a safe and secure hold. Washing machines are important for distributing the load of the bolt and preventing damages to the product being secured. Additionally, rivets are permanent bolts that are suitable for applications where disassembly is not needed. Understanding the differences in between these bolt types is important for selecting the right one for the job, guaranteeing that the link is solid, resilient, and reputable. By selecting the proper bolt kind, you can optimize the performance and long life of your job - Fasteners and Machining.
Picking the Right Materials
Comprehending the importance of selecting the ideal materials is extremely important in making certain the ideal efficiency and integrity of the chosen bolt kinds went over previously. When it pertains to fasteners and machining applications, the material choice plays an important role in identifying the general stamina, sturdiness, deterioration resistance, and compatibility with the desired environment. Various products offer varying buildings that can significantly impact the performance of the fasteners.
Usual materials utilized for fasteners include steel, stainless steel, aluminum, brass, and titanium, each having its special strengths and weak points. Steel is renowned for its high toughness and resilience, making it appropriate for a wide range of applications. Choosing the best material entails thinking about variables such as strength requirements, environmental problems, and budget plan restrictions to make sure the preferred performance and durability of the bolts.
Precision Machining Techniques
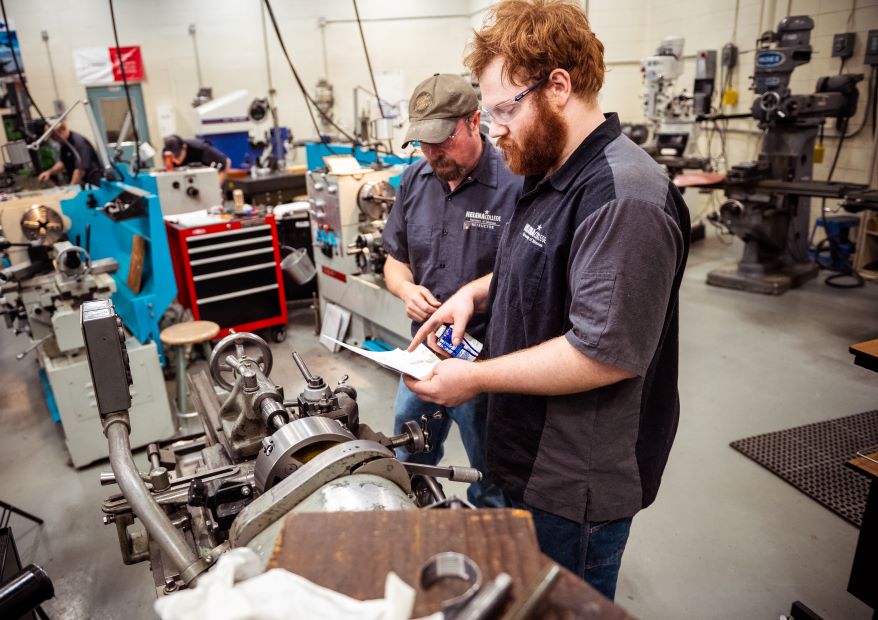
Along with CNC machining, other precision techniques like grinding, turning, milling, and boring play crucial functions in fastener production. Grinding assists attain fine websites surface coatings and tight dimensional tolerances, while transforming is typically made use of to develop cylindrical elements with precise sizes. Milling and exploration operations are crucial for shaping and producing openings in fasteners, ensuring they fulfill exact specs and feature correctly.
Enhancing Speed and Performance
To optimize bolt production procedures, it is crucial to enhance operations and apply effective strategies that enhance precision machining strategies. Automated systems can manage repetitive jobs with accuracy and speed, permitting workers to concentrate on more facility and value-added activities. By incorporating these techniques, suppliers can attain a balance in between speed and precision, inevitably enhancing their affordable edge in the fastener sector.
Quality Control Procedures
Carrying out strenuous high quality control steps is vital in guaranteeing the integrity and consistency of bolt items in the manufacturing process. Fasteners and Machining. Quality control procedures encompass various stages, beginning from the choice of raw materials to the last assessment check over here of the finished bolts. This involves examining factors such as material composition, stamina, and toughness to assure that the fasteners fulfill industry criteria.
Regular calibration of devices and machinery is essential to keep consistency in production and make certain that fasteners fulfill the required tolerances. Implementing stringent methods for identifying and resolving defects or non-conformities is important in protecting against substandard products from going into the market. By establishing a thorough quality assurance structure, manufacturers can maintain the online reputation of their brand and supply fasteners that meet the highest standards of performance and durability.
Verdict
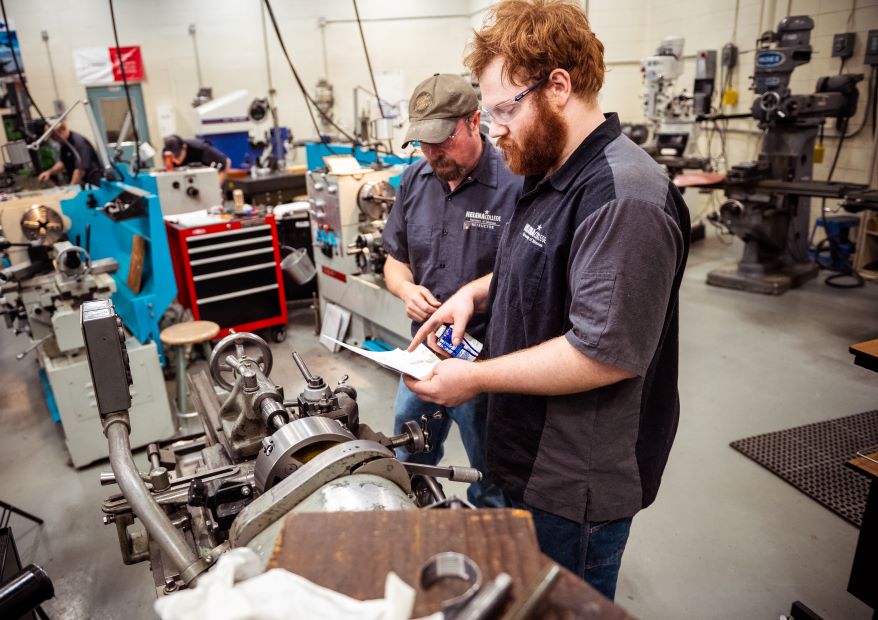
In the detailed world of bolts and machining, the pursuit for accuracy and rate is a continuous obstacle that requires thorough focus to information and critical preparation. When it comes to bolts and machining applications, the product option plays an essential function in figuring out the general stamina, sturdiness, rust resistance, and compatibility with the designated atmosphere. Precision machining includes different advanced methods that ensure the limited try this site resistances and specs required for fasteners.In enhancement to CNC machining, various other precision techniques like grinding, transforming, milling, and exploration play crucial functions in fastener manufacturing.To maximize fastener production procedures, it is essential to streamline procedures and carry out efficient strategies that enhance accuracy machining methods.